What is a forced convection heat transfer plate?
Heat transfer plates are used in so-called “staple systems” to heat the floor by placing heating pipes under the floor.
The aluminum material wraps around the heating pipes, which are then unfolded and attached to the underside of the heated floor.
Heat transfer plates perform three important functions.
- 1. They help carry heat away from the pipes and out through the joist space and floor. (heat transfer)
- 2. They support the plastic heat exchanger tubes.
- 3. They greatly reduce heat loss (return loss) in the downward direction.
There are different opinions on how much aluminum should be used, how thick it should be, and even whether it is necessary.
Here we will provide you with the benefit of our research and experience so you can better understand our advice, or make your own decision.
Heat Transfer – The purpose of your radiant heating system is to generate heat in the form of hot water (we hope in an efficient manner) and then transfer that heat to your floors. Some processes must take heat away from the ducts and apply it to the underside of the floor so the floor can heat the area above. Aluminum is a material that transfers heat very well, but is expensive, its use should be carefully balanced with other methods of doing the same thing, and its application should be optimized for performance and cost-effectiveness.
No Aluminium vs Full Covered Aluminium – Control experiments have shown that covering the pipes with medium/thin gauge aluminium sheets causes the system to release approximately 60% more heat when operating at the same temperature.
If you don’t use aluminum at all, you’ll have to either raise the temperature of the liquid in the tube to a very high level, or use more tubes, or both. Operating plastic heat exchanger tubes at high temperatures is undesirable for reasons of safety, efficiency and longevity.
Aluminium heat transfer plates have a unique and often underappreciated property. Aluminum has a so-called “low emissivity”. The emissivity of aluminum is 0.05, while the emissivity of common materials is 0.95. This means that when aluminum warms, it emits much lower radiant energy (only 5%) than most other materials.
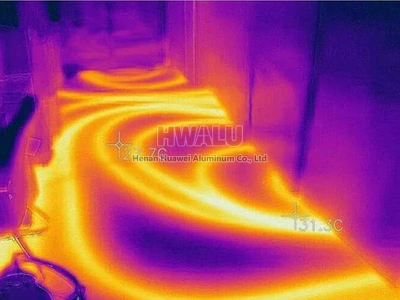
These two pictures show how aluminum sheets can significantly affect the performance of a “stapling” type system.
The image on the left is a photo of the underside of a common floor with radiant heating tubes completely covered with aluminum heating panels.
The image on the right is an infrared heat map of the same situation. Yellow and red represent higher thermal energy emissions, while blue represents lower thermal energy emissions. In this case, all materials are about the same temperature (110 degrees Fahrenheit).
The aluminum plates are about 110°F and dissipate heat downwards (return loss) as if they were only 60°F. This feature has a very positive impact on the overall performance of the “stapling” system, but is usually not valued.
Forced convection heat transfer plate video display